
3D Printing For Film & TV Props
In the early days almost all props for film and television were done by hand using a creative combination of clay, plaster, foam, fabric, wood and other consumer products. Today, prop designers are using 3D printers to create many props and make-up effects. There are clear benefits to using 3D printing technology in the film and television industry.
- Low production costs – hand-made props may require the use of several different materials, creating waste in each, and the labour costs of making the prop are high. The same prop can be 3D printed from just one material without any (or very little) waste. Faster – making a prop by hand can take days or weeks, whereas 3D printing takes only a few hours.
- Reproducible – Multiple copies of props are often required; traditionally, high quality versions are used for close-ups and lower quality versions for background scenes and stunt work. With 3D printing, each copy can be of high quality without the need to spend extra time and money on production.
- Durability – hand-made props are sometimes quite fragile. 3D printed props in nylon and TPU make them tough enough to withstand wear and tear during the shoot. And, when they do break, another model prop can easily be made using 3D printing.
Sci-fi props are by far the most popular items made in Hollywood using 3D printers.The reasons for watching and liking a movie are different for every moviegoer. Among them, the well-made film and television props are the basic elements of a film, and their role in shaping the overall effect of the film is particularly worthy of attention. As a cutting-edge technology, 3D printing undoubtedly provides strong technical support for the manufacture of movie props and brings more possibilities. “The Game of Thrones props team used 3D printing and most of its armour, masks, jewellery and weapons.
In some scenes, the creators avoided the digital route altogether and instead used giant 3D printed dragons. The Jurassic World films did what they did to maximise the recreation of scenes by printing dinosaur remains. Archaeologists and designers worked together to bring the skeletons of various species to life, giving them realistic textures and even including details indicating their sex and age.3D printing is gradually changing the way film props are made, and although in the vast majority of cases it is not yet seen as a completely independent tool, but as a part of a digital solution, as 3D printing becomes more mature and cheaper, its use in the film and television industry is bound to become more and more widespread.
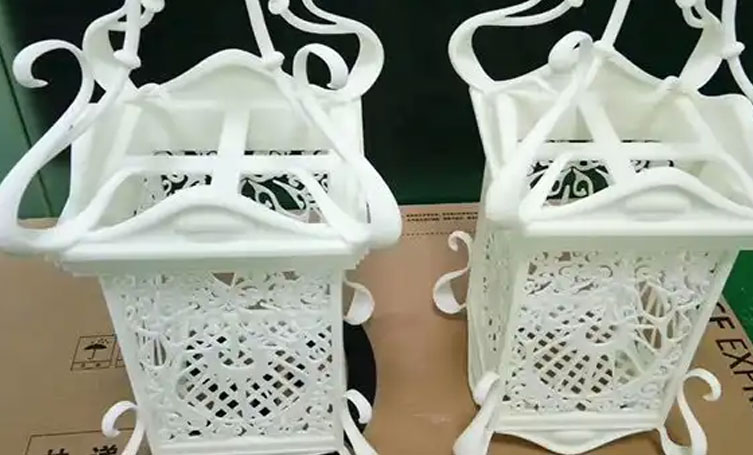
3D Printing For Film & TV Props 3D Printing Services
Wonder Tech is dedicated to providing game-changing solutions- high-performance solutions and faster Film & TV Props 3D Printing services with flexible designs.
We have brought nearly 20 years of materials and manufacturing expertise to every layer of your 3D products to help you in unlocking every dimension of 3D printing techniques.
Direct Prop Making
Traditional props are mostly made by hand, using materials such as clay, wood, foam, silicone, etc. These props often have rough surfaces, simple shapes, little detail and long lead times, especially for science fiction or fantasy films, which are difficult to meet the detail requirements of close-up shots.
Wonder Tech uses 3D printing to produce props directly, which firstly saves the crew a lot of time, and secondly there is almost no limit to the complexity, and the finished product is suitable for close up filming, which can more perfectly reproduce the art and director’s requirements and enhance the visual effect and texture.
Indirect Props
In some cases, the direct production of 3D printed props does not meet the requirements of the film crew, for example due to cost, the need for small batch replication, or the need for special material properties; 3D printing can be used as a tool to create prototypes or moulds, and then use the mould turning process to produce props.
This will absorb the strong modelling ability and short time cycle of 3D printing, while taking advantage of the traditional process in terms of cost, quantity and performance.
Conceptual Model
3D printing is best at turning concepts into reality. For designers, when a concept is presented, whether it is to be upgraded and refined, or to be communicated to the crew for clarification, there is a world of difference in their touch and efficiency between having only 2D floor plans or 3D computer drawings and having a 3D printed physical object.
Whether it’s a new world or a new fantasy creature, making a 3D printed concept model makes the overall communication much easier and more straightforward.
Character Styling, Make-Up
special shapes are often needed in film and television shooting, such as the timeless classic Journey to the West, which was styled under extremely difficult conditions; the hair on the face of the Monkey King was glued on, and the body and face of Porky Pig were silicone clothes and masks.
Whereas now, with the combination of 3D scanning and 3D printing, Wonder Tech can easily capture the full body data of the actors and use the body data as a basis to make various body-fitting looks.
By liberating creativity through digitisation and then outputting it through 3D printing, not only is the styling more realistic and camera-ready, it fits better and the actor-star can suffer less. Without a digital solution, the only way to take a mould is by gluing glue to the body, what a long and painful process. Based on this advancement alone, 3D scanning + 3D printing has a lot of potential in the film and television industry.
Miniature Model
Miniature models are suitable for close-ups or bird’s-eye views in film and television, where close-up details give a realistic feel and a bird’s-eye view of the whole picture gives a macro experience.
3D printed miniature models are highly restored, especially for close-ups, and by alternating physical and digital effects, long and short focal lengths, the whole film will have a more qualitative feel.
Set Design / Destructive Modelling
Creating disaster scenes such as explosions, earthquakes, fires, etc. can be difficult, time consuming and costly, and in many cases it is impossible to actually destroy the original props, even with today’s advanced computer technology, it is still not easy to create realistic disaster scenes with digital effects alone. This is where 3D printing comes into play to help create realistic and destructive models. Once created, flooding, bursting, or wind-blown, they can be made much less difficult to produce.
A classic example of a destructive model is the classic Aston Martin DB5 used in James Bond’s SKYFALL, which needed to be blown up at the end of the film.
Development And Production Of Derivatives
The derivatives market for Chinese films and TV shows is still in a relatively primitive state; in Hollywood, the value generated by derivatives far exceeds the box office, while in China it is the opposite, with the box office taking the lion’s share and derivatives in many cases being a mere fraction or even a gimmick; 3D printing can help change this situation, especially if digital models are used in the early stages, then subsequent derivatives can be quickly developed through 3D printing.