Category | Type | Category | Type |
---|---|---|---|
Maximum build size | 300 x 300 x 300MM | Standard delivery time | 4-6 working days |
Print material | Nylon 12 (PA 12) | Dimensional accuracy | ±0.3%,with a lower limit of ±0.3MM |
Glass filled nylon (PA 12 GF) | Layer height | 0.06 to 0.1MM |
SLS 3D Printing Services
Today thermoplastics have become the dominant material in manufacturing, replacing steel in many applications. Thermoplastics are extremely durable and suitable for long-life applications.Industries can now reap the benefits of 3D printing with this valuable material, extending the use of thermoplastics and gaining the freedom to design beyond the constraints of traditional manufacturing.Injection moulding limits design capabilities, but SLS additive manufacturing gives designers the freedom to achieve more.
Selective Laser Sintering (SLS) is an industrial 3D printing process. In SLS, a laser selectively sears polymer powder particles, fusing them together and building them layer by layer. This type of printing is ideally suited to the manufacture of end-use parts.Wonder Tech is a professional provider of SLS 3D Printing Services with advanced uniontech 3d printer,Raise 3D printer and more. We offer custom SLS 3D Printing for various industries worldwide. Our precision 3d printing machines and experienced team guarantee our incredible custom parts capacity, enabling us to handle the whole stage of the 3d printing process easily from designing, prototyping, manufacturing, to final transportation.
Upload your files, get an immediate quote and be ready for manufacturing in less than 5 minutes
The Applications Of SLS 3D Printing
- Functional prototyping: SLS is ideal for manufacturing functional prototypes from durable, chemically resistant engineering thermoplastics.
- Small batch production: SLS is cost competitive with injection moulding for the manufacture of end-use plastic parts in small batches of up to 300 units.
- High performance components: SLS can be used to produce optimised parts using advanced polymer composites that can be used as replacements for metal parts.
SLS 3D Printing Technology has mature applications in various industries such as automotive, aerospace, consumer electronics, medical, education, and handicraft, and can be widely used for product design and development, including dimensional testing, appearance testing, assembly testing, and functional testing, in addition to small to medium batch manufacturing of final products.
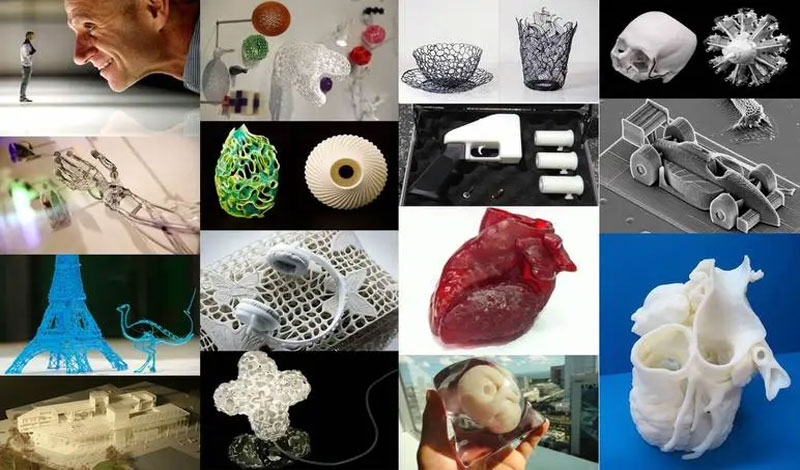
In the automotive industry, for example, the main applications are appearance assessment, structural verification, assembly experiments, ergonomic verification, production of non-standard parts and special performance parts in the automotive field, you can print steering wheels, instrument panels, air conditioning systems, etc. for assembly testing, R & D verification, you can also print customised bumpers, side mirrors and other components directly mounted on the car, which can shorten the R & D testing cycle of new cars and reduce CNC or mould opening costs.
In medical applications, there are mainly manufacturing of rehabilitation/healthcare products and clinical applications such as foot and ankle rehabilitation aids, rehabilitation insoles, rehabilitation cervical pillows, scoliosis orthoses, surgical guides, internal implants, etc.
Applications in consumer electronics are also common, such as various home appliances, power tools, etc.
In addition, SLS is also used in creative products and everyday consumer goods.
SLS 3D Printing Parts And Components
Selective Laser Sintering (SLS) is a 3D printing technology that is part of a family of powder bed fusion processes that produce highly accurate and durable parts that can be used directly for end use, small batch production or prototype prototypes. Typical materials are Plastic Powder, Nylon, Non-metal composite materials, etc.
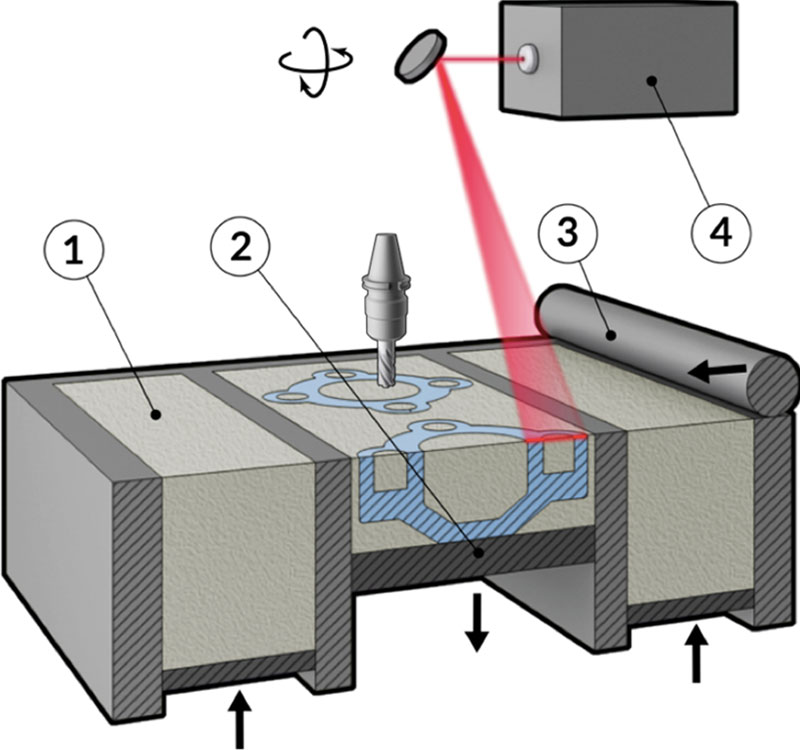
What Is SLS 3D Printing Technology
SLS 3D Printing technology can be used to lay a layer of powdered direct material flat on the upper surface of a formed machined part and heated to a certain working temperature just below the sintering point of the powder. The control management system internally controls the laser beam to scan over the powder layer following the cross-sectional contours of the layer to bring the temperature of the powder up to the melting point, to study the sintering and to achieve it with our formed part companies below Effective bonding.The diagram shows the composition of SLS 3D Printing
- Powdered Materials
- Working Platforms
- Rolls
- Lasers
There are also similarities with the SLA light-curing process (resin printing), meaning that you need to use a laser to cure the entire substance. The difference is that the SLS process uses an infrared laser beam and the material changes from photosensitive resins to those of composite materials such as plastics, waxes, ceramics, metal powders or nylon powders. First, very thin (sub-millimetre) layers of raw material powder are not spread out on the workbench, then the computer-controlled laser beam is scanned by a 30 scanner and the two-dimensional data is layered at a specific speed and energy star density. will be completed. The laser scanned powder is sintered into a solid layer of a certain thickness, while the unscanned areas are loose powder.
The Principle Of SLS 3D Printing
The powder is preheated to a temperature slightly below the melting point and then smoothed out using a roller or scraper. Under computer control, the high intensity CO2 laser selectively sintered parts based on the cross-sectional information of the layers, adhering to the moulded parts below and sintering the next layer when one is complete. When all sintering is complete, the excess powder can be removed and the sintered part can be obtained.
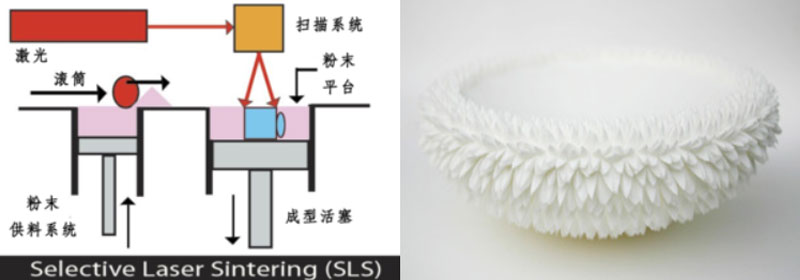
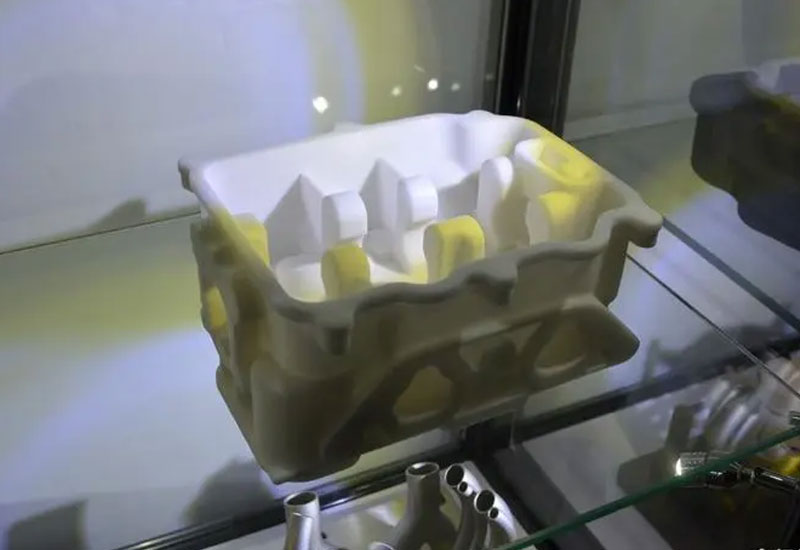
The Advantages Of SLS 3D Printing
- A wide variety of materials are available. Available materials include polymers, metals, ceramics, gypsum, nylon and other powder materials. Metal powder materials, in particular, are one of the developments in 3D printing technology.
- The manufacturing technology process is carried out simply. Due to the relatively large number of available materials, the process according to the different students of the material can be directly affected by the production of complex shapes of prototypes, cavity die build or parts and tools.
- High precision. In general, the tolerance of mm within the overall range of the workpiece.
- No support structure is required, the suspension layer in the lamination process can be directly supported by the un-sintered powder.
- High material utilisation. As no support is required and no base needs to be added, it has the highest material utilisation rate of the several common 3D printing technologies and is relatively inexpensive.