A team at the Fraunhofer Institute for Production Technology (IPT) has introduced an additive manufacturing (AM) process that combines wire-based and powder-based laser cladding. According to the team, this hybrid process produces tool protective coatings that are more wear-resistant, more resource-efficient and cost-effective than traditional laser cladding methods. The hybrid 3d printing process is also more flexible than purely wire-based cladding methods.
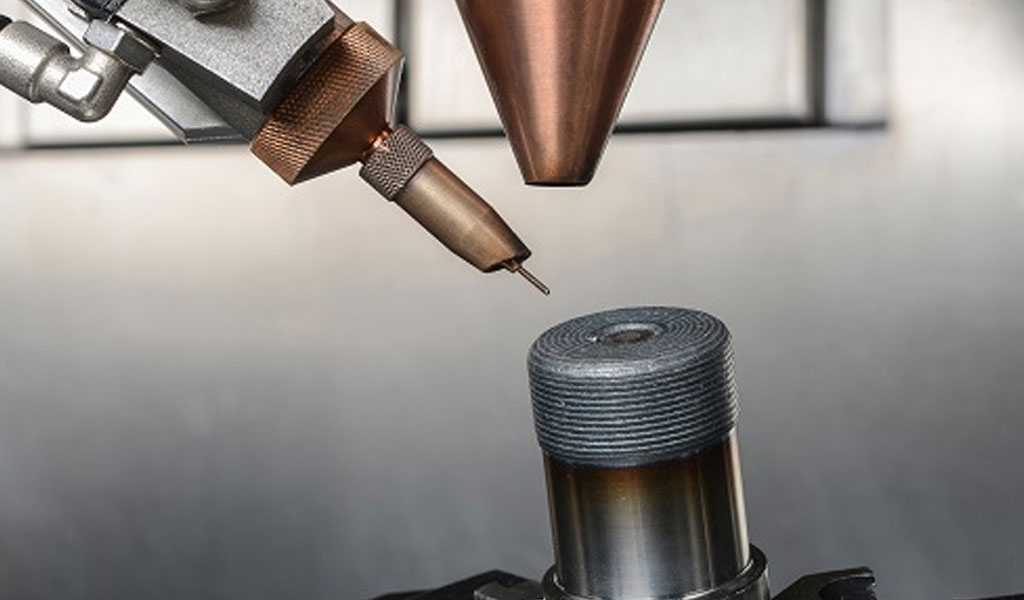
Laser cladding produces 3D structures through laser metal deposition (LMD); during the LMD process, the workpiece surface is heated with a laser beam while filler material in the form of powder or wire is fed into the molten pool area. When the filler melts, it forms a coating on the surface. Structures can be built layer by layer directly on the surface of the workpiece. LMD is an effective method for applying protective coatings, repairing damaged parts, or changing workpiece geometry.
In the hybrid approach to IPT, wire and powder metallurgy materials are processed simultaneously during LMD. The scientists found that by adding hard material particles in powder form to the wire, they could use LMD for the first time to tune important material properties in coatings, such as hardness and toughness.
To determine the best combination of materials for different applications, scientists tested various materials. For wire rods, they chose hot work tool steel with high structural stability and low alloy steel with good weldability. For the powder material, they chose chromium as the carbide-forming and grain-refining element and titanium carbide (TiC) as the hard phase.
By combining powders and wires, scientists are able to tailor the material’s composition for each application. They selectively changed the microstructure of the tool steel and increased the hardness of the coating by adding powder. Adding even a small amount of TiC increases the hardness by 30%.
“With the new process, we can now react quickly and flexibly to different thermal, chemical and mechanical loads, because we can precisely adjust the toughness and hardness,” says project manager Marius Giperich. According to Giperich, the new hybrid process is ideal for minimizing surface wear and extending component life. It is more cost-effective than a pure powder process and allows greater material flexibility than a pure wire process.
The scientists plan to apply their method to the development of other material systems with special properties. They also plan to use the hybrid process for applications such as the machining of forming tools and the treatment of friction and wear layers in hydraulic components.
The IPT team is currently testing the use of the hybrid process in the production of graded coating systems. As DLP 3d printing part of the tests, the team plans to increase the TiC content of the material mixture as much as possible. Since TiC causes high residual stresses, which increases crack susceptibility during welding, the team plans to adjust the TiC content layer by layer.