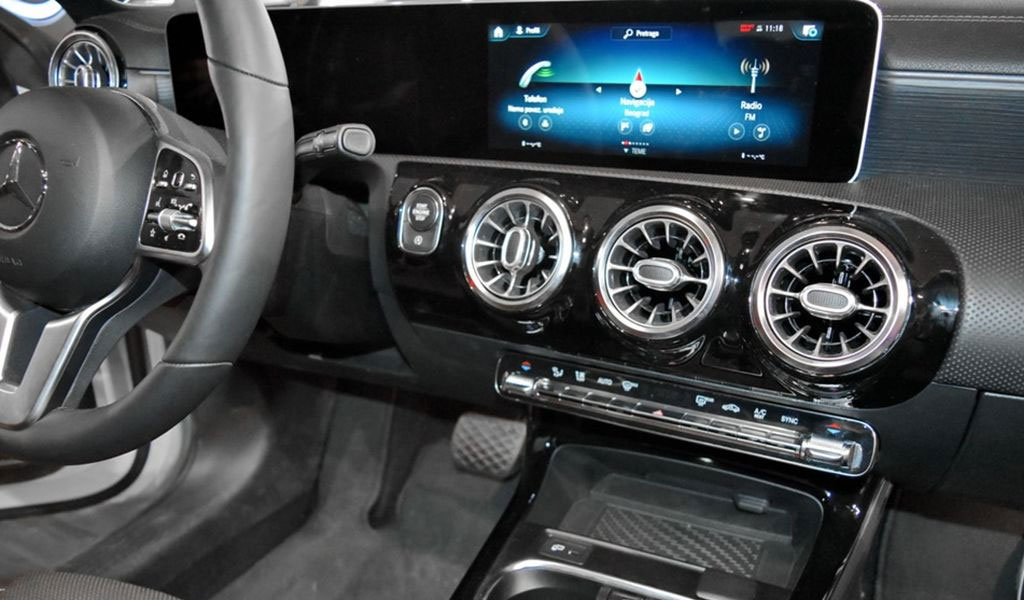
At present, the automotive industry is already the vertical industry with the most 3D printing and cnc machining applications, and judging from the trend, the application of 3D printing in the automotive field will also usher in favorable development conditions.
The first is the issue of the industrial chain. Under the trend of global economicization and the influence of capital’s pursuit of profit, the industrial chain of the automobile industry spreads across many countries around the world. However, under the influence of the epidemic, some parts of the automobile industry have encountered shortages and increased transportation times.
Established automotive powers such as the United States, Germany, and Japan are all facing a broken industrial chain. Except for some high-precision parts produced by their own companies, many other accessories need to be purchased from other countries. Moreover, due to the impact of labor costs and production costs (a certain amount is required to allocate costs), they are also able to re-establish their own supply chains. Therefore, they are currently focusing on researching 3D printing technology, hoping to produce some parts through Titanium Alloy Pen 3D printing technology.
The rapid development of electric vehicles is also conducive to the application of 3D printing technology in the automotive industry. It is expected that by 2035, more than half of new cars sold will be electric vehicles, and in some countries this proportion may reach 80%. In order to seize the market, more than 400 electric vehicles may be launched in the next eight years. This makes the development cycle very tight, and 3D printing has the advantage of quickly manufacturing various prototypes during the research and development stage.
In addition, 3D printed automotive parts can be fully topologically optimized, or directly use parametric generative design to create parts with better performance and lighter weight. Multiple parts can also be combined into one integrated component, reducing installation steps. Especially for electric vehicles, lightweighting is even more important in order to increase their cruising range. Therefore, for some parts, 3D printing may cost more than parts manufactured by traditional processes, but if the later use costs are taken into account, the overall cost will be lower.
In practical applications, engineers also use clever designs to make up for the advantages of 3D printing. Due to the molding technology, 3D printed items will have layers on their surface, which affects their appearance. However, by designing various surface shapes, this shortcoming can be well compensated and the options can be enriched. For example, most of the current car interiors have leather textures. 3D printing can achieve various textures.
Therefore, in general, 3D printing will have good development prospects in the automotive industry.