3D printed titanium alloy pen. The material used is titanium alloy. The flowers are integrally formed with a hollow design, with exquisite design and exquisite workmanship. The surface of the…
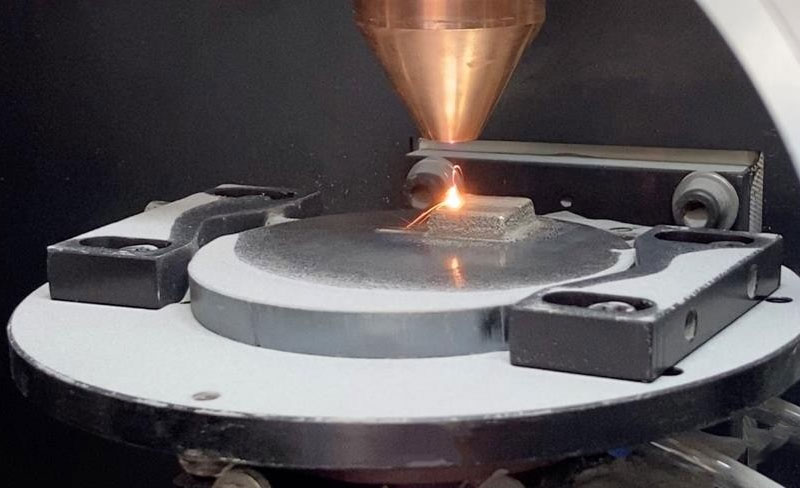
Metal 3D Printing Services
Metal 3D Printing Company has over 10 years experience of Metal 3D Printing, specialising in 3d printing metal parts with small tolerances, complex structural prototypes and high precision.
At present, There are 20 large high-precision metal 3D printers; CNC machining workshop with 16 sets of 3-axis and 5-axis machining equipment, as well as peripheral equipment such as lathes, milling machines, grinding machines, spark machines, vacuum re-moulding machines, etc.The more mature materials for metal 3D printing are titanium alloy (TC4), aluminium alloy (AlSi10Mg), stainless steel (316L), and mould steel (MS1). Stainless steel and aluminium alloys are most commonly used for sample parts, and mould steel is most commonly used for moulded shaped waterways. The products made by metal 3D printing are widely used in various industries such as machinery, medical, communication, electronics, electrical appliances, automotive, military, aerospace, etc.
The Metallic Materials Classification Of Metal 3D Printing
To really process a near-perfect metal part, the equipment carrier is certainly important, but the software, process and materials need to be coordinated with each other. Of course, to manufacture parts or process products with metal 3D printers, you first need to be familiar with the materials, and then talk about precision machinery. Moreover, metal printing, because of the support problem, will lead to later parts can not be processed, may need to consider more material components of the proportional relationship to cater for the printing process of other factors on the impact of material properties. To 3D printing aerospace parts, for example, the metal parts used on aerospace are in extreme environments, with strong corrosion resistance, high temperature resistance, high metal strength, if not familiar with the material characteristics, how to use 3D printing to control the manufacture of metal parts? Therefore, it is particularly important to be familiar with the materials.
However, because of the material properties of metal 3D printing materials themselves, which all have a specific range of applications, the process of selecting a metal 3D printing material is a process of weighing up several factors. Furthermore, 3D printed metal cannot be weighed solely by virtue of the parameters of the metal 3D printer; each metal material has limit points that suit its own characteristics, including application, function, stability, durability, aesthetics and economy are all factors that designers have to consider.
Today, metal 3D printers at home and abroad use metal powders that are generally: tool steel, martensitic steel, stainless steel, pure titanium and titanium alloys, aluminium alloys, nickel-based alloys, copper-based alloys, cobalt-chromium alloys, etc.Don’t know what materials to use? Get a free consultation with a professional engineer on our website today!
The Some Case Studies Of Metal 3D Printing
Wonder takes pride in offering fast, high-quality, tailored projects parts for leading companies in a wide range of industries. Our experience and ISO and IATF certifications ensure quality in every project. We understand the demands of your industry and work with you to ensure they are met and exceeded.Whether you need new product development and validation, custom tooling, etc., Wonder Tech can meet your needs.
3D Printing Titanium Alloy Lampshade
3D printed titanium alloy lampshade. The integrated manufacturing of thin-walled, large-sized, hollowed-out and special-shaped curved surface structures has been realized. The process performance is stable, the surface quality is high,…
3D Printing Western Zhou Dynasty Dake Ding
The full name of the Dake Ding is the Dake Ding of the Western Zhou Dynasty, also known as the Ke Ding and the Shanfu Ke Ding. It is an…
3D Printing Formula Automotive Connector
Realize the precision forming of aluminum alloy parts, the overall size consistency is good, the processing cycle is short, which is conducive to the rapid verification of new products; the…
3D Printing Automotive Rocker
3D Printing Automotive Rocker realizes the precision forming of high-strength steel parts, and 3D printing integrated forming, which reduces the weight by 23% compared with the original design; no post-processing…
3D Printing Arc Welding Table Legs
This structure adopts arc additive manufacturing technology: (WAAM) one-time overall preparation and forming, the structure is a spatial topology structure, the spatial envelope size is 550550900mm, and the minimum hanging…
The Machine Models And Capacity Of Wonder Metal 3D Printer
Applications in military, automotive, electronics, moulds, medical, research institutes, etc.
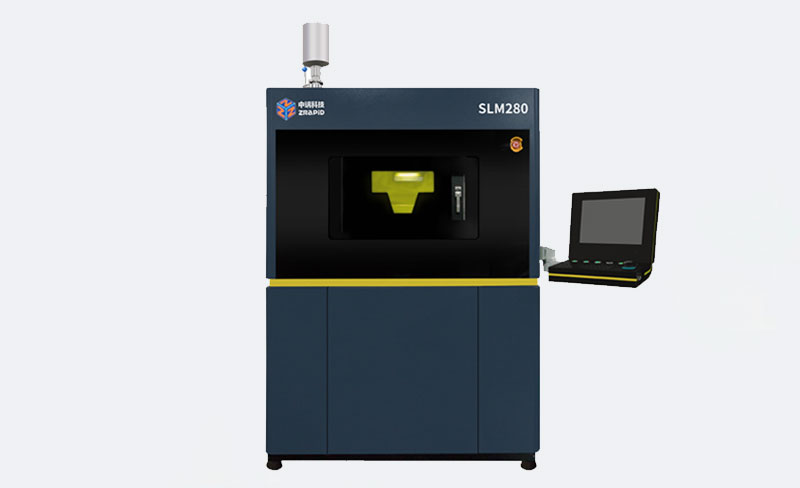
Forming Size: 280mm × 280mm × 380mm
(Including Substrate Thickness)
Forming material: stainless steel, die steel, titanium alloy, aluminium alloy, cobalt-chromium alloy, nickel alloy, copper, etc.
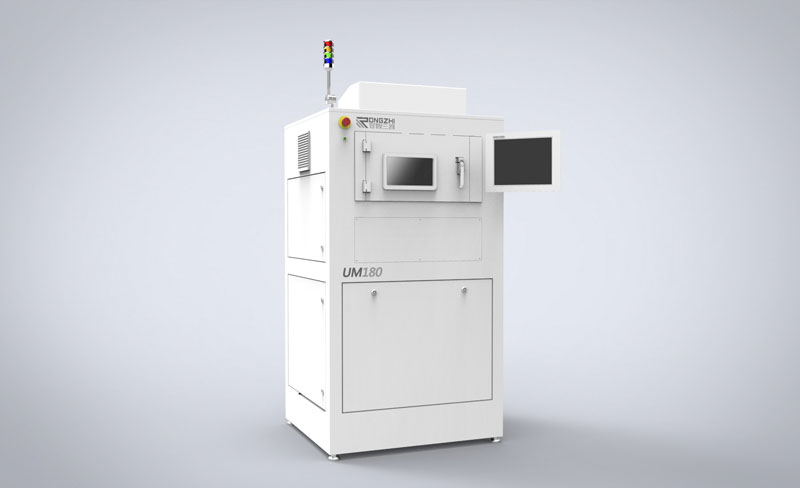
Forming size: 180mm x 180mm x 165mm
(Substrate thickness not included)
Material support: high temperature alloys, titanium alloys, die steel, aluminium alloys etc.
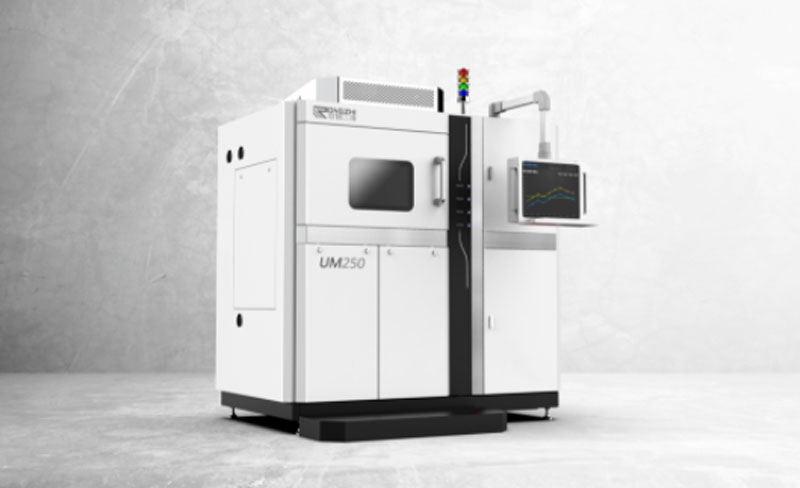
Forming size: 255mm x 255mm x 310mm
(Substrate thickness not included)
Material support: die steel, stainless steel, high temperature alloys, aluminium alloys, titanium alloys etc.
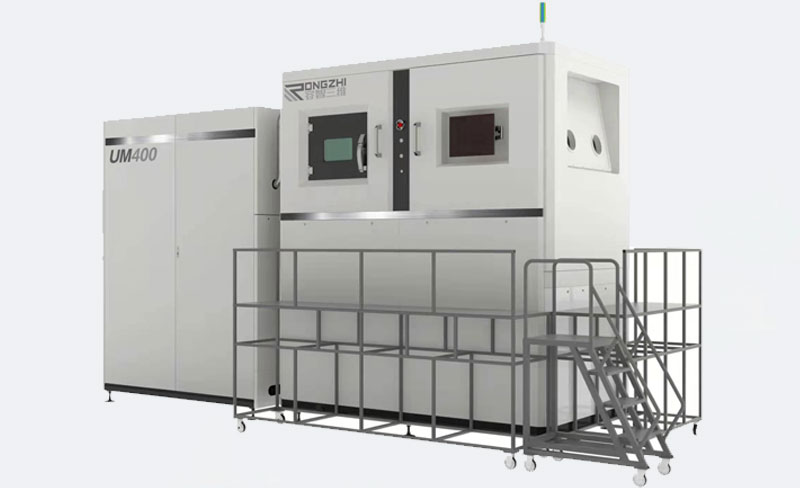
Forming size: 400mm x 600mm x 500mm
(Substrate thickness not included)
Material support: die steel, stainless steel, high temperature alloys, aluminium alloys, titanium alloys etc.
The Appilcations Of Metal 3D Printing
Metal 3D printing Services are used in a wide range of applications, such as petrochemical engineering applications, aerospace, automotive manufacturing, injection moulds, light metal alloy casting, food processing, medical, paper, power industry, jewellery, fashion and many more.We have a team of highly skilled metal printers to solve your problems.
What Is Metal 3D Printing
Metal 3D printing is a technology that belongs to digital thermal processing. The main 3D printing technologies for preparing metals are: selective laser melting/sintering (SLM/SLS), electron beam selective melting (EBSM), laser near net forming (LENS), etc. Compared to traditional processes, metal 3D printing has the advantages of direct forming, no need for moulds, the ability to personalise designs and produce complex structures, high efficiency, low consumption and low cost. However, because it is digital thermal processing, deformation cannot be eliminated and the amount of deformation needs to be controlled from process and experience, and finally post-processed by technologies such as CNC machine tools.
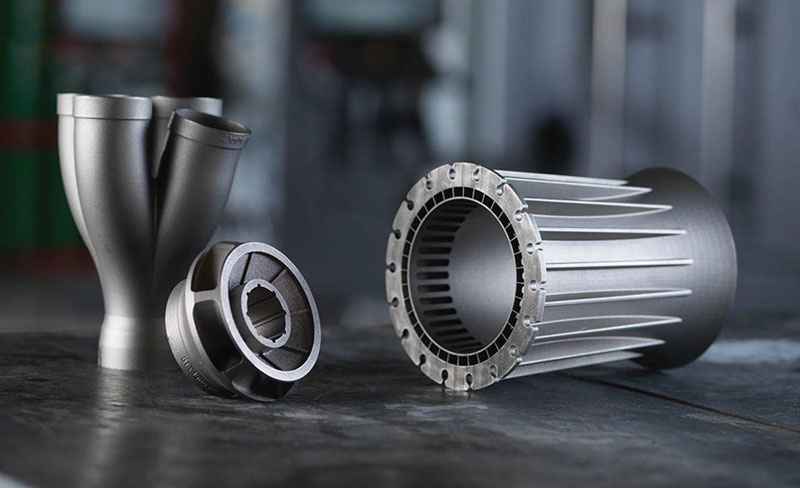
The Advantage Of Metal 3D Printing
- Everything can be printed, any complex structure can be formed in one go without welding, which can save a lot of time.
- A variety of metal materials are available, commonly used materials include stainless steel, aluminium alloy, titanium alloy, mould steel, nano-tantalum powder, nano-tungsten powder, spherical tantalum powder, spherical tungsten powder, cobalt-chromium alloy, nickel-chromium alloy, copper, etc.
- Reduce development costs, help optimise product design, for example, with a complex and reasonable structure instead of the original solid body, so that the finished product weight is lower, but the mechanical properties are better, metal 3D printing technology can effectively shorten the development cycle, manufacturing development comprehensive costs can be reduced by about 50%.
- Stable quality of the printed products, using SLM – laser-selective melting technology, the quality of the printed products is stable, high strength, high precision, ultra-long life.
The The Mnaufacturing Risks Of Metal 3D Printing
As a metal 3D printing source factory, we mainly undertake to print and process customised business, so customers who have printing needs need to provide us with 3D files in STL, STP, STEP and other formats first, our business engineers will be the first time to print the 3D files to print risk assessment, to confirm whether the print production can be achieved, metal 3D printing is theoretically all complex 3D structures Theoretically, all complex 3D structures can be formed in one go without welding, but in the actual production process, due to the performance of the equipment and the size of the print, there are still many structural shapes that cannot be printed, such as those with a wall thickness of less than 0.5mm, or those with an overly complex structure that makes it difficult to remove the support after printing, or those with a large size that may require folding. These are all areas that require a risk assessment before printing.
- Forming Risk: wall thickness, slot width, font size below 0.5mm is not guaranteed to print out, the thread may not be printed out, so the thread is recommended to use tapping, not recommended to print directly (internal and external threads are the same).
- The Risk Of Deformation: metal printing after high temperature sintering, due to stress, some slender parts, thin-walled parts, shell parts and other structures will have the risk of deformation, the advantage of metal printing is that the structure of complex parts can be integrated into the shape, the accuracy and surface effect is not as good as machined;.
- The Risk Of Tolerance: metal printing equipment laser scanning printing is actually very high precision, the error is less than 0.05mm, due to high temperature sintering molding after thermal expansion and contraction, the tolerance of the final product will become larger, generally speaking within 50mm of the product printing tolerance ± 0.1mm, the larger product printing tolerance depending on the drawing, generally 0.1% of the length; high precision requirements need to provide 2D plan, and mark the tolerance requirements, or leave the machining allowance in advance, and then improve the accuracy through secondary finishing with.
- Assembly Risk: Assembly parts need to be reminded to send assembly assembly diagram, before delivery will be assembled before sending, such as no reminder is not responsible for the assembly, the need to assemble the product clearance bit one side need to put 0.15mm, local assembly requirements of high (such as bearing holes / diameter / plane assembly bit) to leave machining allowance in advance, and then through the secondary finishing with.
- The Appearance Of Risk: this colour printing finished surface pitting in Ra7-16 or so, the conventional surface treatment for sandblasting after grinding, surface roughness effect inferior to the machined, there may be support to go unclean or grinding after the residue of the marks; polishing or plating parts may be caused by the support surface grit residue; metal printing material after treatment with the same traditional materials can be followed by secondary processing treatment. However, the aluminium alloy material can only be oxidised in a sub-black colour, and the effect may be worse than that of machined parts.
- Delivery Risk: because metal 3D printing will exist a certain probability of print failure, failure to replay will have caused the possibility of delivery delays.
How To Create a Metal 3D Printing Parts
Although, 3D printing is a free-structure manufacturing technology, there are many machining methods needed to circumvent the pain points of 3D printing post-processing. The CNC machine tool machining techniques used in traditional manufacturing are therefore particularly important and complement 3D printing in that different products can be shaped to perfection by varying the dominant manufacturing process when utilising the two technologies. Here we take a look at the process of metal 3D printing.
Step 1
placing an order (takes about 10-30 minutes)
After receiving the quotation and related risks from the salesman, you can choose to cooperate with Wonder. After receiving the order, the salesman will immediately record the order in the system and schedule the production, Wonder now has sufficient equipment capacity, generally the order placed in the morning can be arranged on the same day, the order placed in the afternoon will be arranged on the next day, special circumstances are negotiable.
Step 2
Engineering drawing processing (approximate time 4-12 hours)
The engineering department will process the engineering 3D drawings upon receipt of the production dispatch order. The engineering department will sort the drawing files that need to be printed with different materials according to the production order, then adjust the placement according to the size and shape of the product, add support, modify or delete support according to the printing needs, etc. No special requirements are generally printed by multiple product collages, adjusted and then processed by layering and slicing.
Step 3
machine adjustment and commissioning (approx. 1-4 hours)
After receiving the print file from the engineering department, the print production department selects the appropriate equipment according to the availability of the machine, imports the print file, adjusts the print parameters according to the requirements of the printed material, installs the print substrate for the product and preheats it. Our equipment currently supports 3 different printing parameters for the same version of the printed product, which improves printing efficiency and ensures the accuracy of the product for special requirements.
Step 4
Start printing (approx. 10-100 hours)
We use SLM selective laser sintering technology, processing equipment equipment for high-precision SLM selective dual laser head fusion 3D printing equipment, the production of molding parts not only precise size accuracy, high strength, high density, its mechanical properties and other aspects of performance is very good, the comprehensive performance of processing equipment in the domestic is one of the best.
After adjusting the parameters and preheating the equipment to start formal printing, printing powder scraper will first lay a thin layer of metal powder, laying powder thickness of 10-40, can be adjusted according to needs, and then metal 3D printing equipment, high-energy laser according to the graphics selective scanning sintering metal powder, so that it becomes the desired three-dimensional shape of the slice, scanning printing completed a layer, the substrate down a layer, and then repeat The process of laying down the powder for printing is repeated, layer by layer, until the product is printed. Laser spot diameter of 0.1mm, scanning a layer of the time used according to the product structure and print area of about 20-120 seconds, all the time to complete the print due to different heights will vary greatly, because we now all existing equipment are dual laser head printing, so in the comprehensive printing efficiency will be twice as fast as most of the peers, many domestic peers with metal printing equipment are still single Many of our domestic counterparts are still using metal printing equipment with a single laser head.
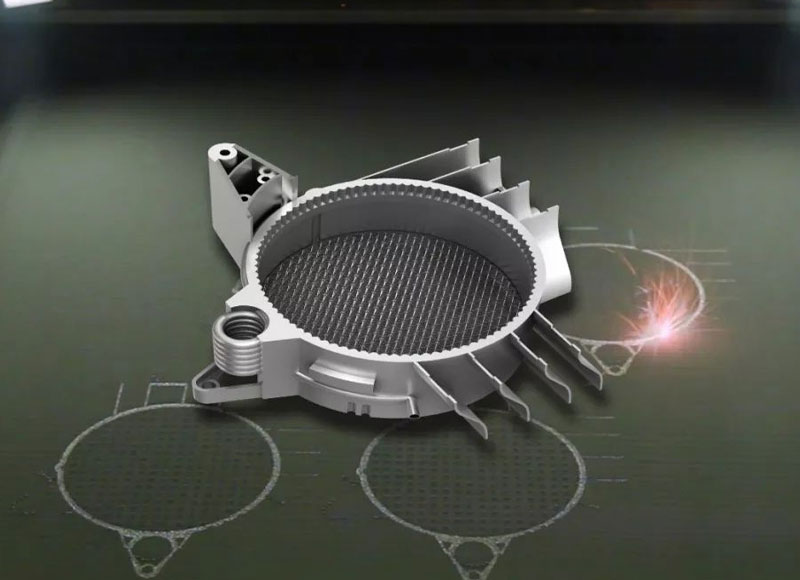
Step 5
Powder removal from the machine (approx. 0.5-1 hour)
When the product is printed, the machine stops automatically, after the nitrogen is evacuated and the natural cooling, the print substrate slowly rises to its initial position and the machine operator carries out manual powder cleaning and dismounting operations, after which the workpiece substrate is marked with a number and sent to the heat treatment workshop with a production instruction sheet.
Step 6
Heat treatment (approx. 2-6 hours)
The workpiece is sent to the heat treatment workshop, according to the different materials and sexual requirements, adjust the oven temperature parameters, commonly used heat treatment parameters are: stainless steel for 840 ℃ baking 1 hour + 500 ℃ baking 4 hours, aluminum alloy for 300 ℃ baking 2 hours and then air cooling, mould steel for 490 ℃ baking 6 hours; the workpiece is cooled and sent to the wire cutting workshop.
Step 7
Line cutting separation (approx. 2-6 hours)
The workpieces sent to the wire-cutting workshop are arranged according to the delivery schedule of the production order. Wonder has purchased a large number of wire-cutting machines in order to compress the delivery time, which currently takes between 2 and 3 hours for aluminium and 3 to 4 hours for stainless steel, depending on the size of the contact point between the workpiece and the substrate. The workpieces are separated and sent to the manual handling workshop together with the corresponding production orders.
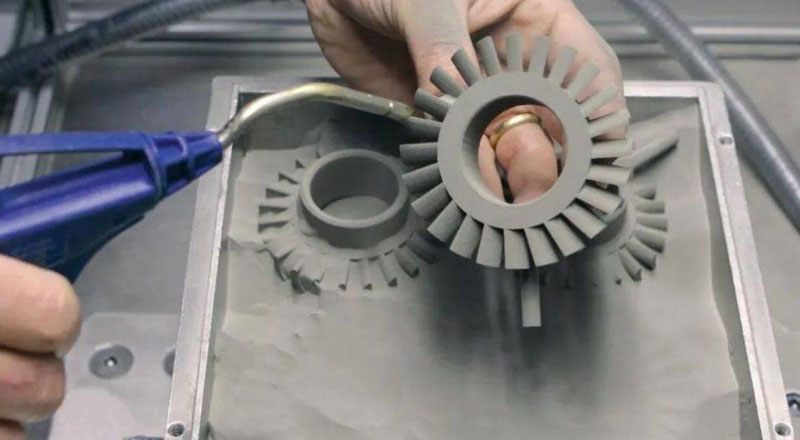
Step 8
Manual surface treatment (approx. 12-48 hours)
The workpieces sent to the manual treatment workshop will be surface treated according to the requirements of the production order, and usually need to be de-supported first, the manual master uses suitable tools to remove the additional support when printing and forming, and then use coarse sanding tools to sand the support position smooth, and then use fine sanding tools to fine sand the product surface, to correct the defects of the product, to polish the product surface smooth, no special requirements Products with no special requirements are sent to the sandblasting workshop for surface sandblasting treatment. Workpieces with special treatment requirements, such as polishing, electroplating and painting, will be uniformly polished and sent to the quality inspection department after treatment is completed.
Step 9
Quality inspection (approx. 1-4 hours)
For workpieces sent to the quality inspection department, quality inspection will be carried out according to the 3D drawings and floor plans provided by the customer for dimensional and appearance inspection, products that meet the customer’s requirements will be released and the salesman will be notified to arrange for delivery, products that fail the quality inspection will be returned to the handicraft department for rework or re-doing.
Step 10
Shipping logistics (takes about 2-48 hours)
After the salesman receives the qualified products, he will arrange the express logistics according to the customer’s requirements.Compared to the traditional CNC hand-printing process, the use of metal 3D printing has a very prominent advantage in terms of material utilisation.The whole process takes about 3-6 days for regular products, and for rush jobs it is negotiable. The reason is that the final down time is determined by the larger product.